Alternative Construction Technologies
The following alternative construction technologies - Insulated Concrete Forms, Structural Insulated Panels, and Panelized Home Building Systems - are all excellent alternatives to traditional construction for building a home at either a lower cost, higher energy efficiency, stronger construction, quicker construction time, or a combination of these!
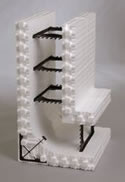
Insulated Concrete Forms
As the saying goes, “Build a better mousetrap and the world will beat a path to your door.” The popularity of building homes with Insulated Concrete Forms (ICF) seems to be proving the old adage true. Of course, for home builders, erecting forms and pouring concrete walls is nothing new, at least below grade. But the advent of lightweight, stackable, interlocking forms that also incorporate interior and exterior insulation has opened the market for ICF for virtually all exterior wall applications.
We offer 120+ home designs adapted for ICF construction using these brands:
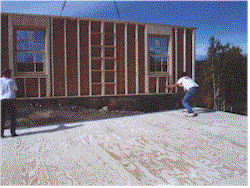
Panelized Home Building Systems
In the high-tech approach known as panelized construction, pre-engineered wall sections are produced for a new home in factory-controlled conditions, then shipped complete to the building site for final construction. A panelized home can be weather tight in just a few days.
Leading panelized home manufacturers offer tremendous flexibility in design and can provide any amenities desired in a new home. Some panelized manufacturers work through networks of general contractors (professional home builders). Others deal directly with home buyers looking to build their own home.
Please note: While Design Basics takes great pride in designing homes to be built using these building systems, Design Basics neither builds homes nor supplies products for these building systems. These pages are for informational purposes only.