Structural Insulated Panel (SIP) Construction
In the story of the three little pigs, the first two brothers were interested in building their homes quickly, so they could get on with enjoying life. Too bad they didn’t look into building with Structural Insulated Panels (SIPs – High-quality foam core panels that are strong, energy-efficient, and suitable for many residential and commercial building applications). That big, bad wolf would have had to look elsewhere for dinner!
According to industry estimates, SIPs are the fastest growing segment of panelized construction. Typically constructed of a rigid foam core sandwiched between Oriented Strand Board (OSB), SIPs capitalize on the advantages of building homes panelized, namely, faster construction, consistent high quality, reduced waste, and, in many cases, lower overall costs. Additionally, SIPs raise the ante by offering increased strength and energy efficiency, plus even shorter construction cycle times.
Insulspan structural panels are high-quality foam core panels suitable for many residential and commercial building applications. They are solid, one-piece structural components that can be used in walls, floors, and roofs. Each panel is made of an Expanded Polystyrene (EPS) core bonded between two outer layers of rugged OSB. lnsulspan structural panels form a strong, versatile building shell that will significantly shorten construction times, compared with conventional building methods. Because of their energy-saving characteristics, they make an extremely cost-effective building material.
Please note: While Design Basics takes great pride in designing homes to be built using Structural Insulated Panels, Design Basics neither builds homes nor supplies products for these building systems. These pages are for informational purposes only.
EPS Foam Core
Each Insulspan panel contains one pound of EPS for every cubic foot of core. Higher densities are available for special applications. Depending on the strength and energy-efficiency your application requires, you can specify four standard thicknesses for panels.
EPS is an inert, stable cellular plastic with superior insulating qualities. Unlike many other foam products, EPS is ozone-friendly – no CFCs are used in the production of lnsulspan panels. Other characteristics of EPS include:
Structural Integrity: EPS retains its shape indefinitely. It will not shrink, decompose, or disintegrate due to age or weather.
Thermal Stability: The insulating value of EPS does not decrease with age.
Toxicity: EPS is formaldehyde-free.
Low Water Absorption: EPS has a closed cell structure. Its water absorption level is so low that moisture and the elements will not significantly affect its insulation values.
Permanence: EPS is an inert, organic material. It provides no nutritive value to plants, animals, or microorganisms. It will not rot and is highly resistant to mildew.
Flammability: Like many construction materials, EPS is combustible. It should not be exposed to flame or other ignition sources. However, you can expect a building made with Insulspan products to survive a fire that would completely destroy a stick-built home. The panels have passed rigorous fire endurance tests required by national codes, and their solid core construction eliminates the chimney effect caused by hollow stud walls. See technical bulletins on the Insulspan site for further application information.
Exterior and Interior Skins
The oriented strand board skins on Insulspan structural panels are exterior rated Exposure I by the American Plywood Association. Exterior phenolic resin permits the panels to be used with normal construction delays.
Energy Efficiency and Comfort
lnsulspan panels decrease cooling and heating costs even more than their high R-rating would seem to indicate because they form a solid thermal envelope around the structure, uninterrupted by the typical studs, sills, or headers. This substantially reduces air infiltration compared with conventional construction techniques. The panels’ solid core of insulation also eliminates the convection looping that can occur in the gaps and spaces typical in batt insulation.
Insulspan panels provide stable performance year after year. Their efficiency generally allows heating and cooling equipment to be downsized, reducing initial capital costs and operating costs.
Strength and Durability
The strength of Insulspan panels has been proven through rigorous structural testing required by national code authorities, plus their actual performance through more than 20 years of use. The beam-like properties of Insulspan panels can make them 2-3 times stronger than typical stick-built structures.
Adapting Home Plans to SIP Construction
Almost any home design can be modified to be built with SIPs. Of course, if a home design would be complex to frame traditionally, it will be complex to build with SIPs. Also, while SIPs can make excellent roof systems, complex, sophisticated roofs are often trussed or stick-built. The versatility of marrying SIPs and traditional construction methods on the same home is a welcome feature of SIP construction.
SIP walls are often thicker than standard framed walls. For example, Insulspan markets SIP walls that are 4-1/2″ thick or 6-1/2″ thick. As compared with traditional 2” x 4” or 2” x 6” exterior framing, rooms in a home with one or more exterior walls will finish out slightly smaller. A further consideration is that wider jamb extensions will need to be ordered for windows and exterior doors. Despite their thickness, the panels are relatively lightweight, meaning cantilevers are no problem when building with SIPs. And, SIPs adapt easily for differing foundation types.
Factors to Consider
Pre-planning is one of the keys to the success of SIP construction. Plumbing and electrical runs need to be pre-determined, so the manufacturer can accommodate these needs. The quality (level of detail and thoroughness) of the shop drawings the SIP supplier produces is very important, as they address questions up front before they can become problems on site.
Cost
Many factors come into play when building a home panelized. Because they are engineered and built in a factory, panelized walls (and roof panels) are more expensive initially than buying raw materials for conventional construction. However, the resulting savings in terms of site labor, material waste and clean-up fees, and shorter construction timeframes offset much, if not all, of the cost of the panels. SIPs may cost more than other panels due to the insulation component, but again that cost is largely offset when compared to adding the insulation on site. In fact, SIP walls typically carry a much higher insulation factor, which requires additional expense to bring a conventionally framed home up to the same energy efficiency of a SIP home.
Structural Insulated Panel Industry Relationships
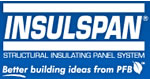